Parametric design and optimisation of wind turbines
The design procedure of wind turbines requires a techno-economical assessment of each of the candidate designs produced along the iterations of the optimisation loops. The scope of this analysis depends on the design stage of the product and on the technology (onshore, offshore fixed or floating) employed to produce electricity.
We offer support on the development of your products, applying latest design procedures and techniques to optimise your baseline concepts under a holistic approach. System components, rotors, controllers, towers, substructures and foundations or mooring systems are considered as a full system in the automated process. Client defined or eureka provided design process and techno-economical assessment content is implemented in the iterative optimisation process. As result, you will get more knowledge on the correlations that relate performance, cost and the design variables of your concept together with an optimised version (less cost and better performance) of your product.
Reduce your products time-to-market with us, be more competitive!
Parametric design and analysis processes
Our in-house developed CAE solutions (wedado) to parametrise any wind turbine and its components with a high level of fidelity (onshore, offshore fixed and floating) implements the tools to perform the required analyses to design these systems. Complemented with client defined or eureka! provided/built design procedures and the designs exploration and optimisation capabilities developed, results in a very powerful tool.
Considering site conditions and client preferred standards, the system is submitted to component-level specific iterative design processes. Although components are designed in cascade, the procedures and analyses consider the system as a coupled system. Meanwhile design requirements are fulfilled, the design continues the process workflow, in any case, the data produced is used to fed a database for further analyses. When requirements are fulfilled, the dynamic behaviour of the overall system in the wind farm is assessed considering the Design-Driving Load Cases (DDLCs) of each component being designed. If results are satisfactory, wake analysis of the wind farm is performed to calculate the Annual Energy Production (AEP) with low uncertainty.
After completing the required retro-feeding loops between components-level (blue circle in figure below) and wind farm (red circle in figure below) design and analysis procedures, a summary of the Key Indicators (KIs) is generated.
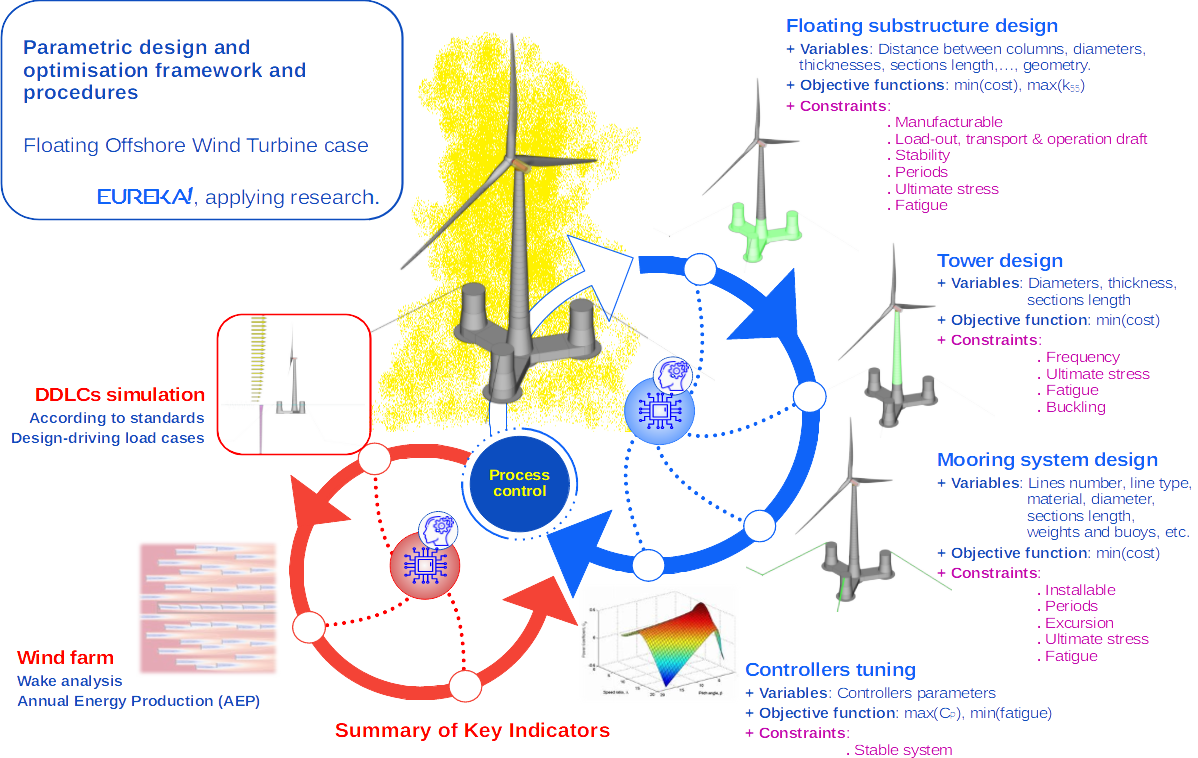
Design space exploration
Profiting from the automated design and analysis procedure implemented, this is exploited. A set of design variables is defined for each of the components to design and that will modify the system. Design restrictions to ensure industry limits and recommendations (for example, metal plate thicknesses) and/or client defined ones are also considered. The resulting design space is explored to quantify the impact of the design variables on the Key Indicators (KIs). eureka! employs Design of Experiment (DoE) techniques to measure and visualise the correlations between parameters.
Optimisation of the wind turbine
At this stage, most relevant design variables identified during the design space exploration are taken into account in a machine-driven optimisation process. From the KIs, the most relevant ones are classified as objective functions which will be minimised/maximised. Therefore, robust optimisation algorithms are a key factor to handle a muti-variable and multi-objective optimisation where designs are submitted to such demanding design and analysis procedures.
Not so overhelming...
Site conditions
-
- Definition of site conditions or
- select from eureka! database
Baseline wind turbine
-
- Definition of the baseline wind turbine according to the level of detail desired or
- provide the support structure and select a RNA and controller from eureka! database.
Standards
-
- Choose the Classsification Society of your preference
- Choose the Classsification Society of your preference
Design variables, restrictions and objectives functions
-
- Definition of the design variables affecting system components
- Definition of the design restrictions that constrain the design space
- Definition of the objective functions to optimise (cost, production, lifetime, etc.)
Design process
-
- Definition of the design process you want to follow or
- improve/built it supported by our knowledge or
- choose a generic one from our database so we can adapt it to your technology